So you want to make your own diecast models? That’s awesome! It might sound intimidating, but with the right approach and a bit of patience, you can create incredibly detailed and personalized miniature replicas of your favorite cars, trucks, or even fantastical vehicles. This isn’t about mass production; it’s about the joy of crafting something unique.
Choosing Your Method: Resin Casting vs. 3D Printing
There are two primary ways to create the body of your diecast: resin casting and 3D printing. Resin casting offers a smoother, more refined finish, ideal for capturing intricate details. 3D printing, on the other hand, provides greater design flexibility and allows for complex shapes but might require more post-processing to achieve a smooth surface.
Resin casting typically involves creating a master model (often from sculpting clay or a 3D printed model), making a mold from silicone or other mold-making materials, and then pouring resin into the mold. This process can be messier but often yields superior results.
3D printing allows for direct creation of the model using a 3D printer. Different materials like resin or plastic are available, each affecting the final finish. You’ll need access to a 3D printer and design software, but the potential for unique designs is immense.
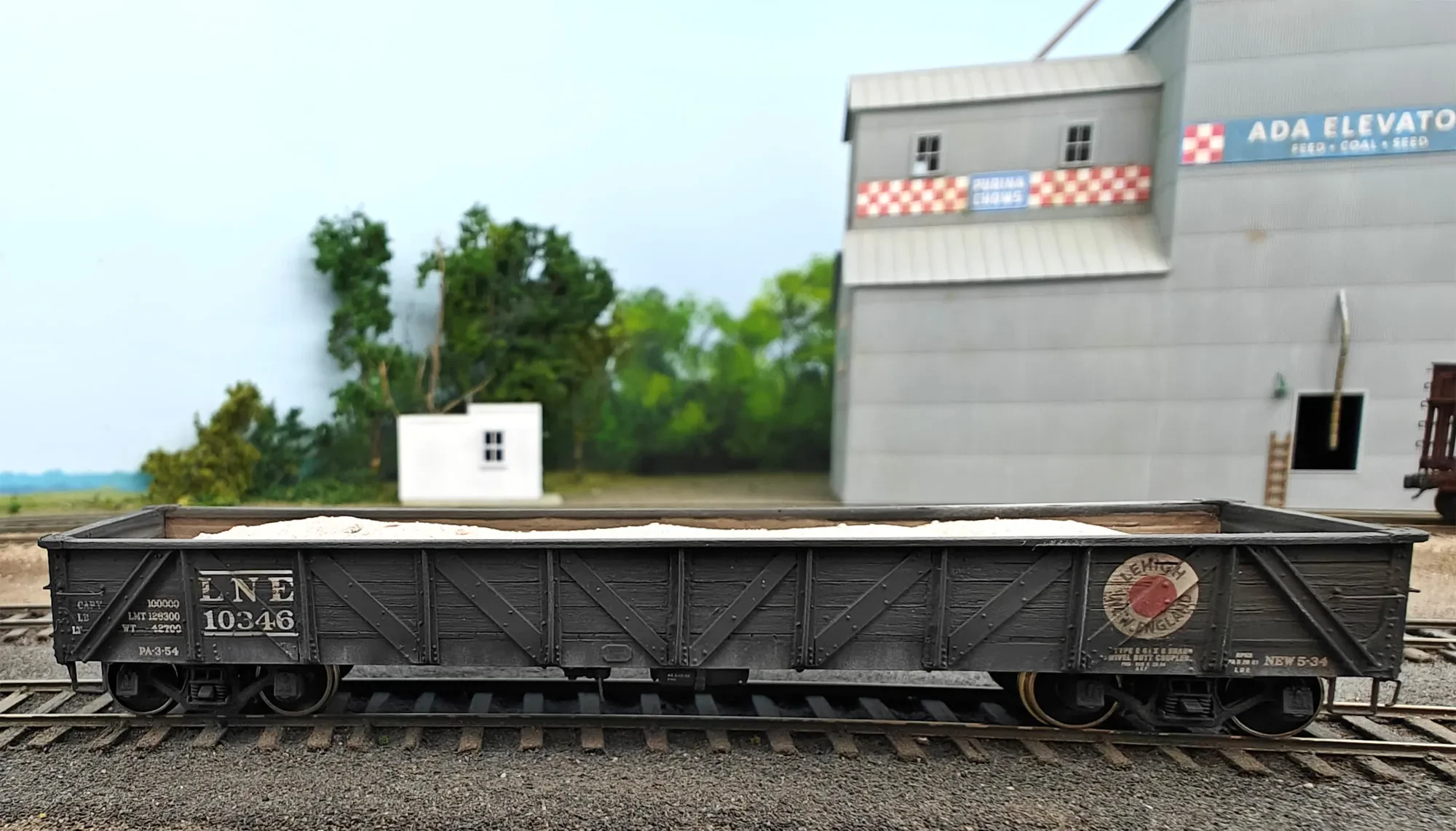
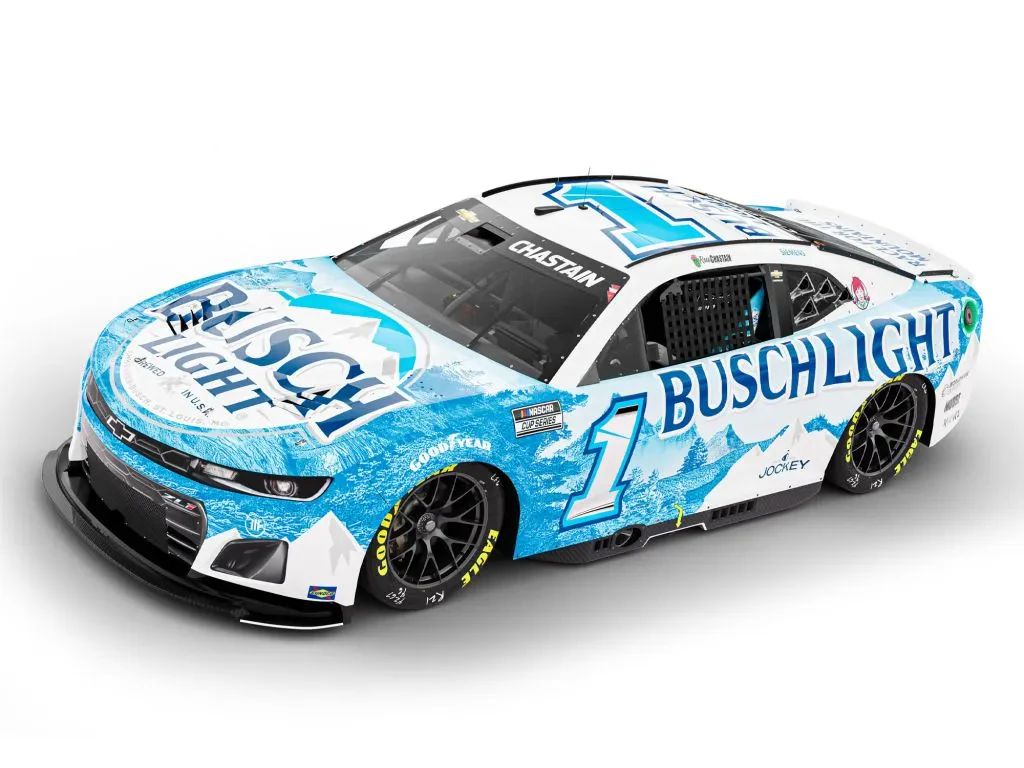
Designing Your Diecast
Whether you’re using resin casting or 3D printing, design is key. For resin casting, you might sculpt your model from clay or use a digital design program to create a 3D model that you can then 3D print as a master for your mold. For 3D printing, you’ll need to design your model entirely digitally using CAD software.
Consider the level of detail you want to include. Tiny details will be more challenging to achieve, particularly with resin casting. Think about the scale of your model and plan your design accordingly.
Software Options
- Blender (Free and open-source)
- Fusion 360 (Subscription based, powerful)
- Tinkercad (Beginner-friendly, browser-based)
Creating the Mold (Resin Casting Only)
Once you have your master model, creating the mold is crucial. Silicone rubber is a popular choice for mold making due to its flexibility and ability to capture fine details. You’ll need to carefully prepare your master model (likely by applying a release agent) before pouring the silicone into a mold box surrounding your model. Follow the instructions for your specific silicone carefully.
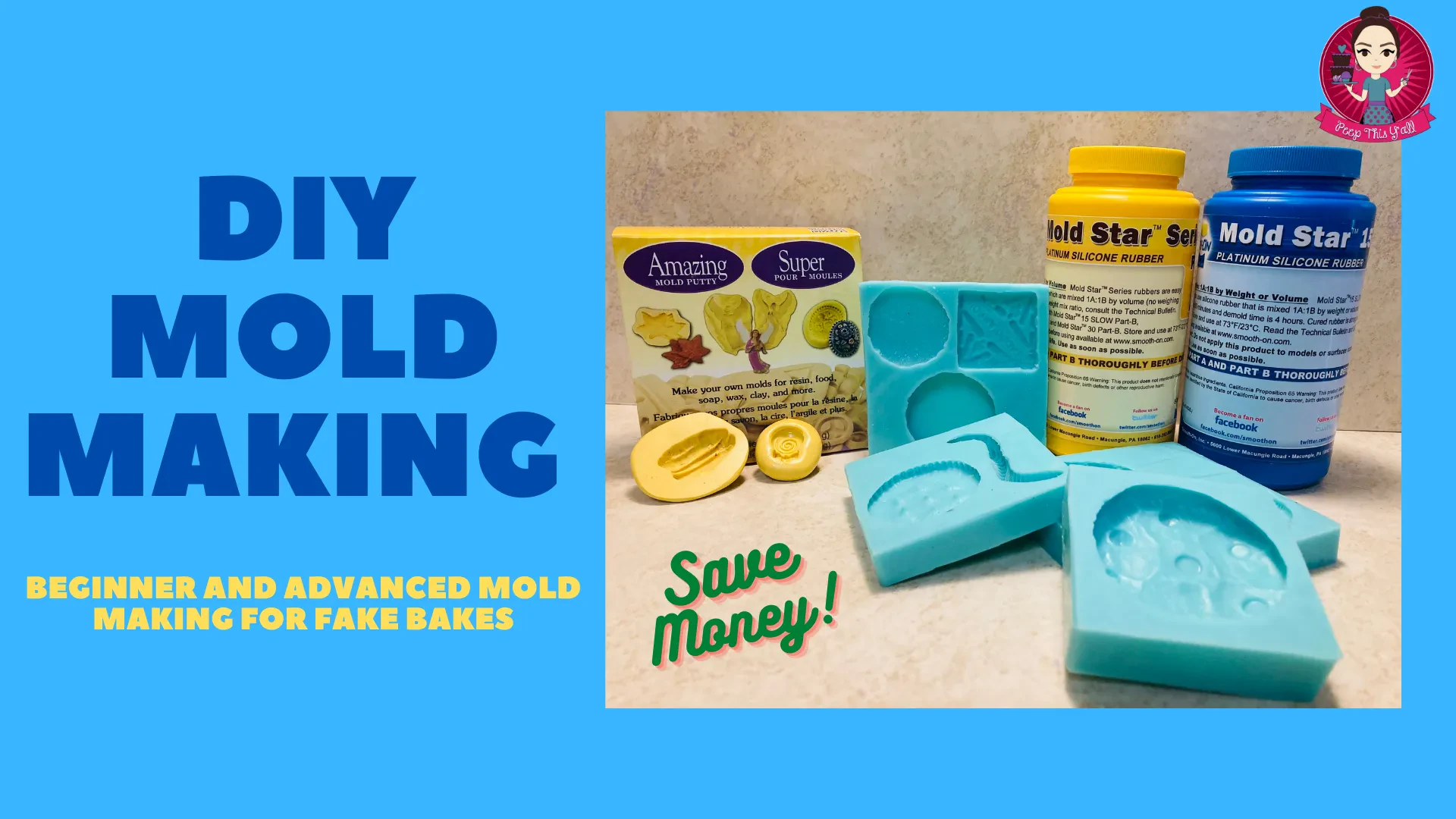
Casting and Finishing
After your mold cures, it’s time to pour the resin. Work in a well-ventilated area and follow the resin manufacturer’s instructions carefully. Once the resin cures, carefully remove your diecast from the mold. You’ll likely need to do some cleanup and sanding to remove any imperfections.
Depending on your chosen method, you may need to clean up the model with sandpaper, remove supports from 3D printing, or fill small gaps. Once satisfied with the body, you can start adding details like wheels, windows, and paint.
Adding Details and Painting
This is where your diecast really comes to life. You can use small scale wheels, plastic sheets for windows, and a wide range of paints to bring your vision to reality. Take your time and be patient, applying thin coats of paint for a professional look.

Remember, creating your own diecast models is a journey. Don’t be discouraged by imperfections – embrace the process and celebrate the unique character of your handmade creations. With practice and experimentation, you’ll improve your skills and create stunning models you’ll be proud of.